Identification and Assessment of Hazards in the Workplace
Introduction:
Ensuring a safe working environment is of utmost importance to protect the well-being of employees and prevent accidents and injuries. The second category of workplace safety involves the identification and assessment of hazards. This article aims to discuss the process of identifying and assessing hazards in the workplace, including physical, chemical, and biological hazards, and the utilization of various forms and methods for recording and reporting these hazards.
- Identification of Physical, Chemical, and Biological Hazards:
The first step in the hazard identification process is to recognize the presence of hazards in the workplace. Hazards can be classified into three main categories:
– Physical Hazards: These include factors such as noise, radiation, heat, pressure, vehicles, electrical and mechanical equipment, and more.
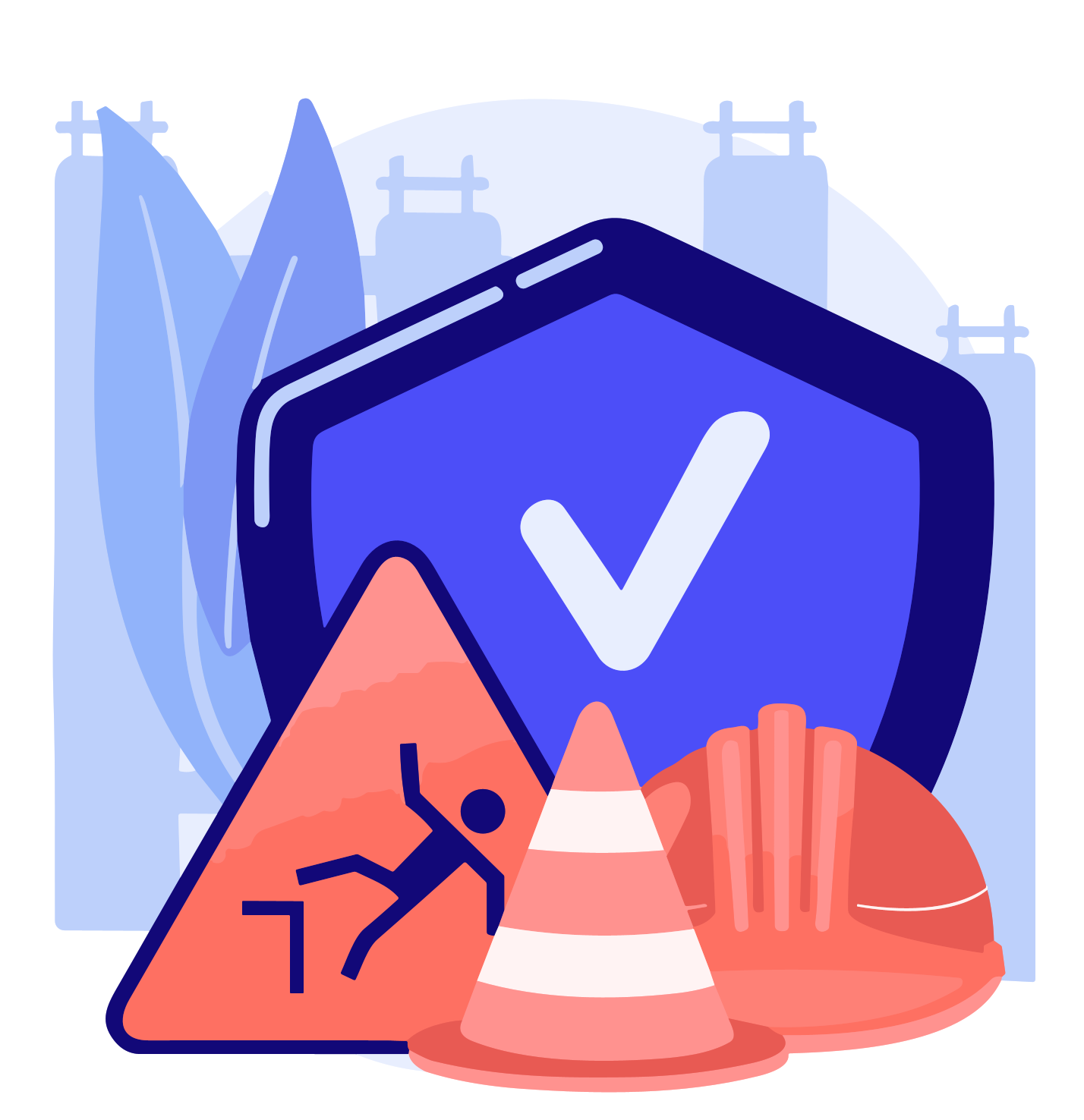
- Noise:
Excessive noise levels can pose a significant physical hazard in the workplace. Exposure to high noise levels over an extended period can lead to hearing damage and other health issues. Industries such as manufacturing, construction, and aviation are particularly prone to high noise levels due to heavy machinery, power tools, or aircraft operations. Employers should conduct noise assessments to identify areas or job tasks with excessive noise and implement measures such as engineering controls (soundproofing, barriers), administrative controls (job rotation, limiting exposure time), and personal protective equipment (earplugs, earmuffs) to minimize the risk to employees.
- Radiation:
Radiation exposure is another critical physical hazard that can occur in certain work environments. Workers in industries such as healthcare, nuclear power, and radiography may face potential exposure to ionizing radiation. Prolonged or excessive exposure to ionizing radiation can lead to various health issues, including radiation sickness and an increased risk of cancer. It is essential for employers to implement radiation safety measures, including proper shielding, monitoring equipment, training on safe practices, and adherence to regulatory guidelines to protect workers from harmful radiation.
- Heat and Cold:
Extreme temperatures can also present physical hazards in the workplace. Exposure to high temperatures can lead to heat-related illnesses, such as heat exhaustion or heatstroke, particularly in industries like construction, agriculture, and foundries. On the other hand, exposure to extreme cold temperatures can result in frostbite, hypothermia, or other cold-related injuries, often seen in outdoor work environments or freezer storage facilities. Employers should provide proper training on recognizing and preventing heat and cold-related illnesses, promote hydration and rest breaks in hot environments, and provide appropriate protective clothing and heating facilities in cold environments to mitigate these physical hazards.
These physical hazards require careful assessment, implementation of preventive measures, and regular monitoring to ensure the safety and well-being of workers in the respective work environments.
– Chemical Hazards: Chemical hazards encompass toxic, flammable, explosive, corrosive, or reactive substances present in the workplace. These may include solvents, pesticides, acids, bases, and other hazardous chemicals.
- Toxic Substances:
Chemical hazards often involve toxic substances that can cause harm or illness when workers are exposed to them. These substances can include solvents, pesticides, heavy metals, and certain gases. Inhalation, ingestion, or skin contact with these toxic substances can lead to acute or chronic health effects, including respiratory problems, organ damage, neurological disorders, or even cancer. Employers must properly identify and label hazardous chemicals, provide Material Safety Data Sheets (MSDS) or Safety Data Sheets (SDS) for each substance, and implement control measures such as ventilation systems, personal protective equipment (PPE), and employee training to minimize exposure and ensure worker safety.
- Flammable and Explosive Substances:
Flammable and explosive substances pose a significant risk in various industries, including manufacturing, laboratories, and construction. These substances, such as flammable liquids, gases, or dust, can ignite easily and lead to fires or explosions. Improper storage, handling, or use of these substances, or failure to implement appropriate safeguards, can result in severe injuries, property damage, and even fatalities. Employers must conduct proper risk assessments, implement fire prevention measures, establish safe storage and handling procedures, provide fire extinguishers and emergency response plans, and educate employees on safe practices to mitigate the risks associated with flammable and explosive substances.
- Corrosive Substances:
Corrosive substances are another category of chemical hazards commonly found in workplaces. These substances, such as strong acids or bases, can cause severe damage to the skin, eyes, or respiratory system upon contact. Industries that handle or work with corrosive substances include manufacturing, laboratories, and cleaning services. Employers must provide appropriate personal protective equipment, such as gloves, goggles, or face shields, ensure proper storage and handling procedures, and establish emergency response protocols in case of accidents or spills involving corrosive substances. Training employees on safe handling practices and implementing engineering controls, such as fume hoods or ventilation systems, can further minimize the risks associated with corrosive substances.
Ensuring proper identification, handling, and control of chemical hazards is crucial for protecting employees from the potential health risks associated with exposure to toxic, flammable, explosive, or corrosive substances. Compliance with safety regulations, ongoing risk assessments, and thorough employee training are essential components of managing chemical hazards in the workplace.
– Biological Hazards: Biological hazards refer to living organisms or their byproducts that can cause harm or disease in the workplace. Examples include bacteria, viruses, fungi, allergens, and bloodborne pathogens.
- Bacteria and Viruses:
Biological hazards in the form of bacteria and viruses can pose significant risks to workers’ health in various industries, including healthcare, laboratories, and food handling. Exposure to pathogenic bacteria, such as Salmonella or E. coli, can lead to foodborne illnesses, while viruses like influenza or COVID-19 can cause respiratory infections. Proper hygiene practices, including handwashing, sanitization, and disinfection protocols, are essential in preventing the spread of bacteria and viruses. Additionally, personal protective equipment (PPE) like gloves, masks, and gowns can help reduce the risk of exposure to these biological hazards.
- Fungi and Mold:
Fungi and mold can be present in workplaces with poor ventilation, water damage, or high humidity levels. Industries such as construction, agriculture, and manufacturing may encounter biological hazards in the form of mold spores that can cause respiratory issues, allergies, or fungal infections. Employers should address moisture issues promptly, conduct regular inspections for mold growth, and implement appropriate remediation measures to prevent the proliferation of fungi and mold in the workplace. Adequate ventilation, proper cleaning practices, and the use of respiratory protection when necessary are crucial in mitigating the risks associated with these biological hazards.
- Bloodborne Pathogens:
Workers in healthcare settings, laboratories, or emergency response fields may be exposed to bloodborne pathogens, such as HIV, hepatitis B, or hepatitis C. Contact with infected blood or bodily fluids through needlesticks, splashes, or other direct contact can lead to serious infections. Employers must establish comprehensive infection control programs, including the use of engineering controls (safety devices, sharps containers), proper training on safe work practices, availability of personal protective equipment (gloves, face shields), and protocols for post-exposure management. Regular communication and education on bloodborne pathogens are essential in raising awareness and preventing exposure incidents.
Biological hazards present unique challenges in the workplace due to the potential for disease transmission and health risks. Employers must prioritize preventive measures, such as hygiene practices, proper ventilation, appropriate PPE, and employee education, to ensure the safety and well-being of workers when dealing with bacteria, viruses, fungi, allergens, and bloodborne pathogens. Regular risk assessments, monitoring, and adherence to relevant regulations and guidelines are vital in managing and minimizing the risks associated with biological hazards in the workplace.
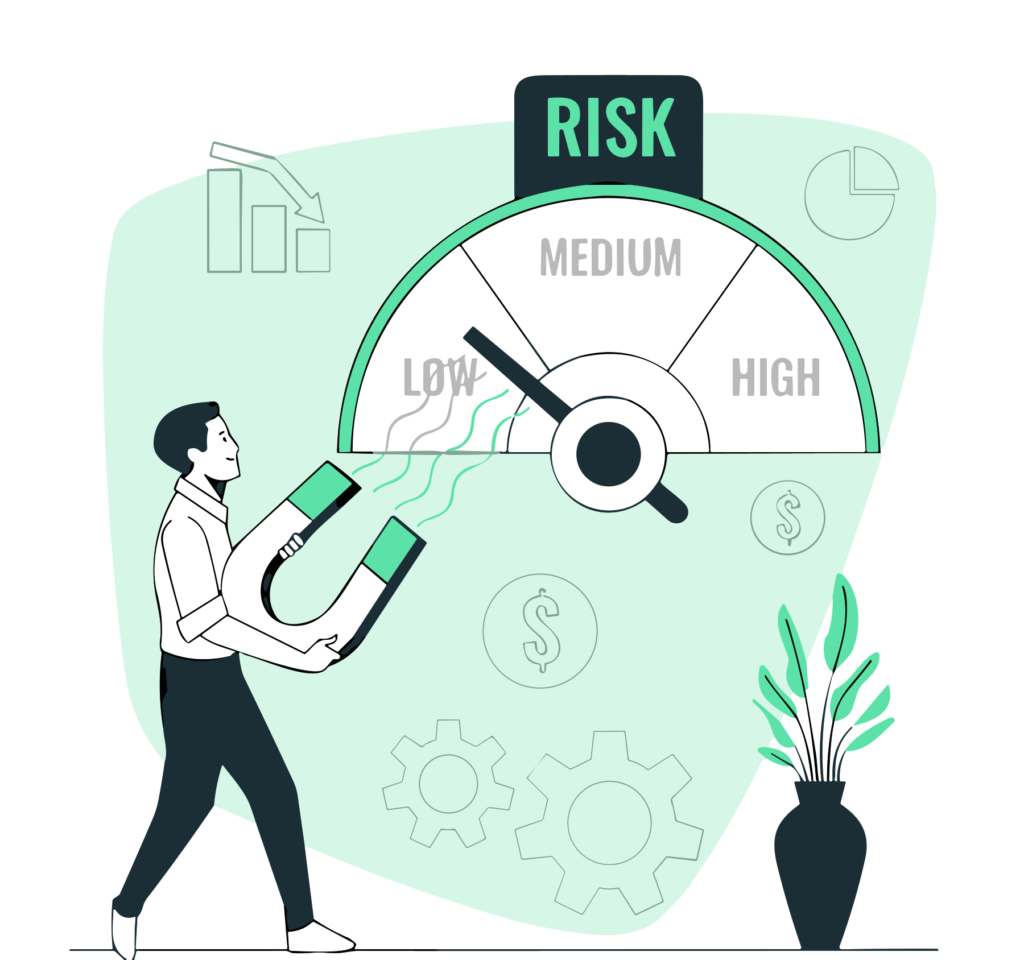
- Risk Assessment and Prioritization of Hazards:
Once hazards have been identified, the next step is to assess the risks associated with each hazard and prioritize them accordingly. Risk assessment involves evaluating the probability and severity of potential harm or damage resulting from exposure to the hazard. This information helps employers and safety professionals determine the level of risk posed by each hazard and allocate appropriate resources to mitigate them effectively.
After identifying the hazards present in the workplace, the next crucial step is to conduct a comprehensive risk assessment. Risk assessment involves a systematic evaluation of the potential risks associated with each identified hazard. It aims to determine the probability and severity of harm or damage that could result from exposure to the hazard.
During the risk assessment process, employers and safety professionals gather relevant information to assess the level of risk associated with each hazard. This information may include historical incident data, scientific research, industry guidelines, and input from employees who work directly with the hazards. By considering these factors, they can gain a better understanding of the hazards’ characteristics and potential consequences.
The risk assessment process typically involves two main components: probability and severity. Probability refers to the likelihood of an incident or harm occurring due to exposure to the hazard. It takes into account factors such as frequency of exposure, duration, and the effectiveness of existing control measures. Severity, on the other hand, assesses the potential impact or harm that could result from an incident. It considers factors such as the extent of injuries, property damage, and the potential for long-term health effects.
By evaluating both probability and severity, employers and safety professionals can assign a risk level to each hazard. This risk level helps prioritize hazards based on their potential impact and guides the allocation of resources for mitigation efforts. High-risk hazards that have a significant probability and severe consequences are typically given the highest priority for immediate action, while lower-risk hazards may receive less immediate attention.
The risk assessment process is an ongoing activity and should be regularly reviewed and updated as new hazards are identified or changes occur in the workplace. It is also important to involve employees in the risk assessment process, as they often have valuable insights and firsthand knowledge of the hazards they encounter in their day-to-day work.
By conducting thorough risk assessments and prioritizing hazards accordingly, employers and safety professionals can make informed decisions about implementing control measures, allocating resources, and developing safety strategies. This proactive approach helps ensure the effective mitigation of risks, ultimately creating a safer working environment for employees.
- Use of Forms and Methods for Recording and Reporting Hazards:
To ensure comprehensive hazard management, various forms and methods are employed to record and report identified hazards. These tools facilitate the systematic documentation and communication of hazards, enabling better analysis and decision-making. Common forms and methods include:
– Hazard Reporting Forms: These forms are used by employees to report identified hazards to the appropriate authorities within the organization. They typically include details such as hazard description, location, potential consequences, and recommended control measures.
Hazard reporting forms serve as a vital tool for employees to report identified hazards within the organization. These forms provide a structured way for employees to communicate their observations and concerns regarding workplace hazards to the appropriate authorities, such as supervisors, safety officers, or the designated safety committee. By using hazard reporting forms, employees contribute to the overall safety and well-being of the workplace.
When completing a hazard reporting form, employees are typically asked to provide detailed information about the identified hazard. This includes a clear description of the hazard, its location within the workplace, and any relevant factors that contribute to its presence or occurrence. The form may also require employees to assess the potential consequences or risks associated with the hazard, such as the likelihood of injuries, property damage, or environmental impact.
In addition to describing the hazard, employees may be encouraged to provide suggestions or recommended control measures to mitigate or eliminate the hazard. These recommendations can include engineering controls, administrative controls, or the use of personal protective equipment. By involving employees in the hazard reporting process, organizations can tap into their firsthand knowledge and experience to identify practical solutions for hazard control.
Hazard reporting forms play a crucial role in maintaining a proactive approach to workplace safety. They facilitate the timely identification, documentation, and resolution of hazards, helping to prevent accidents, injuries, and potential disruptions to operations. Organizations should ensure that hazard reporting forms are easily accessible to employees, provide clear instructions for completion, and guarantee confidentiality and non-retaliation for those reporting hazards.
Once a hazard is reported using the appropriate form, it should trigger a systematic review and response process within the organization. This may involve conducting further investigations, implementing control measures, assigning responsibilities for hazard mitigation, and monitoring progress until the hazard is adequately addressed. Timely and effective follow-up on hazard reports demonstrates the organization’s commitment to safety and encourages employees to actively participate in hazard identification and reporting.
By utilizing hazard reporting forms as part of their safety management system, organizations create a culture of continuous improvement and empower employees to actively contribute to a safer work environment. Regular review and analysis of reported hazards can provide valuable insights for identifying trends, implementing preventive measures, and promoting a proactive safety culture throughout the organization.
– Risk Assessment Forms: Risk assessment forms aid in the evaluation of hazards by assessing their likelihood, severity, and overall risk level. These forms help in determining the priority for implementing control measures and monitoring the effectiveness of risk reduction strategies.
Risk assessment forms are valuable tools used to evaluate hazards within an organization. These forms facilitate a structured approach to assessing the likelihood, severity, and overall risk level associated with identified hazards. By using risk assessment forms, organizations can systematically analyze hazards and make informed decisions regarding the implementation of control measures and monitoring strategies.
When completing a risk assessment form, individuals responsible for assessing the hazard typically consider various factors. These factors may include the probability or likelihood of the hazard occurring, taking into account aspects such as the frequency of exposure, the number of individuals at risk, and the effectiveness of existing control measures. The form may also prompt evaluators to consider the severity of potential consequences, including the extent of injuries, property damage, or environmental impact.
In addition to evaluating likelihood and severity, risk assessment forms often provide a framework for determining the overall risk level. This can be achieved by combining the likelihood and severity ratings or using a predefined risk matrix. The risk level helps prioritize hazards based on their potential impact, allowing organizations to allocate resources effectively and address higher-risk hazards promptly.
Risk assessment forms also facilitate the identification of appropriate control measures. Based on the risk level determined through the assessment, the form may prompt evaluators to recommend specific control strategies. These strategies can include engineering controls (e.g., implementing machine guards), administrative controls (e.g., developing standard operating procedures), or the use of personal protective equipment. These recommendations guide the organization in implementing effective risk reduction measures.
Furthermore, risk assessment forms serve as a valuable reference for monitoring the effectiveness of implemented control measures. By documenting the initial risk level and control measures recommended, organizations can regularly review and update the forms to track changes in risk levels over time. This ongoing monitoring allows for the identification of emerging hazards, the evaluation of control measures’ effectiveness, and the implementation of necessary adjustments to mitigate risks.
Effective utilization of risk assessment forms supports a proactive approach to risk management. By consistently assessing hazards, organizations can prioritize resources, implement appropriate control measures, and monitor risk reduction efforts. Regular review and analysis of risk assessment forms contribute to continuous improvement in safety practices and help create a culture of risk awareness and prevention within the organization.
Overall, risk assessment forms provide a structured and systematic approach to evaluating hazards, determining risk levels, and guiding decision-making processes for implementing control measures. They are essential tools for maintaining a safe and healthy work environment and ensuring the ongoing management of risks within an organization.
– Incident Reporting Forms: Incident reporting forms are used to document and report workplace accidents, injuries, or near-miss incidents. They capture critical information related to the event, contributing factors, and recommendations for preventing similar incidents in the future.
Incident reporting forms play a vital role in documenting and reporting workplace accidents, injuries, or near-miss incidents. These forms provide a standardized means for employees and witnesses to report incidents and capture essential information related to the event. By using incident reporting forms, organizations can gather valuable data that helps identify trends, analyze root causes, and develop preventive measures to enhance workplace safety.
When completing an incident reporting form, individuals involved in or witnessing the incident are typically asked to provide detailed information about what occurred. This includes a description of the incident, including the date, time, and location. The form may also prompt individuals to provide a narrative of the events leading up to the incident, contributing factors, and any immediate actions taken to mitigate the situation.
Incident reporting forms often include fields to document injuries sustained, property damage, or other impacts resulting from the incident. In the case of near-miss incidents where no injuries occurred, the form allows for the documentation of potential consequences that could have resulted if the circumstances had been slightly different. This comprehensive documentation helps organizations understand the severity of the incident and its potential implications.
Furthermore, incident reporting forms provide an opportunity to identify underlying causes or contributing factors that led to the incident. The form may include sections to capture information about equipment failure, procedural deficiencies, human error, or environmental factors. This information helps organizations conduct thorough investigations to determine the root causes and implement corrective actions to prevent similar incidents from occurring in the future.
In addition to documenting the incident itself, incident reporting forms often include sections for recommendations or suggestions to prevent future incidents. Individuals completing the form can provide insights into potential control measures, improvements to procedures, or additional training needs. These recommendations contribute to the organization’s continuous improvement efforts and help foster a proactive safety culture.
Incident reporting forms also serve as a valuable database for tracking and analyzing incident trends. By regularly reviewing and analyzing the information captured in these forms, organizations can identify patterns, common hazards, or recurring issues. This analysis provides valuable insights for developing targeted safety initiatives, implementing preventive measures, and allocating resources effectively.
By utilizing incident reporting forms as part of their incident management system, organizations prioritize the timely reporting and documentation of workplace incidents. This proactive approach allows for thorough investigations, the identification of corrective actions, and the continuous enhancement of safety practices. It also promotes a culture of accountability and encourages employees to actively participate in incident reporting, ultimately creating a safer work environment for all.
Conclusion:
The identification and assessment of hazards in the workplace are essential components of effective safety management. By recognizing physical, chemical, and biological hazards, conducting risk assessments, and utilizing appropriate forms and methods for recording and reporting, organizations can establish a safer working environment. This proactive approach allows for the implementation of control measures, employee training, and continuous improvement initiatives to mitigate risks and prevent accidents, promoting the well-being of workers and the overall success of the organization.
