Personal Protective Equipment and Safety Gear: Ensuring Workplace Safety
Ensuring the safety and well-being of workers is of paramount importance in any workplace. Personal protective equipment (PPE) and safety gear play a crucial role in safeguarding individuals from potential hazards and minimizing the risk of accidents and injuries. This article highlights the significance of utilizing PPE, including items such as footwear, hearing protection, goggles, and masks, along with the importance of employing protective equipment such as gloves, helmets, and covers. Additionally, the regular maintenance and inspection of safety equipment are emphasized to ensure their effectiveness in mitigating workplace risks.
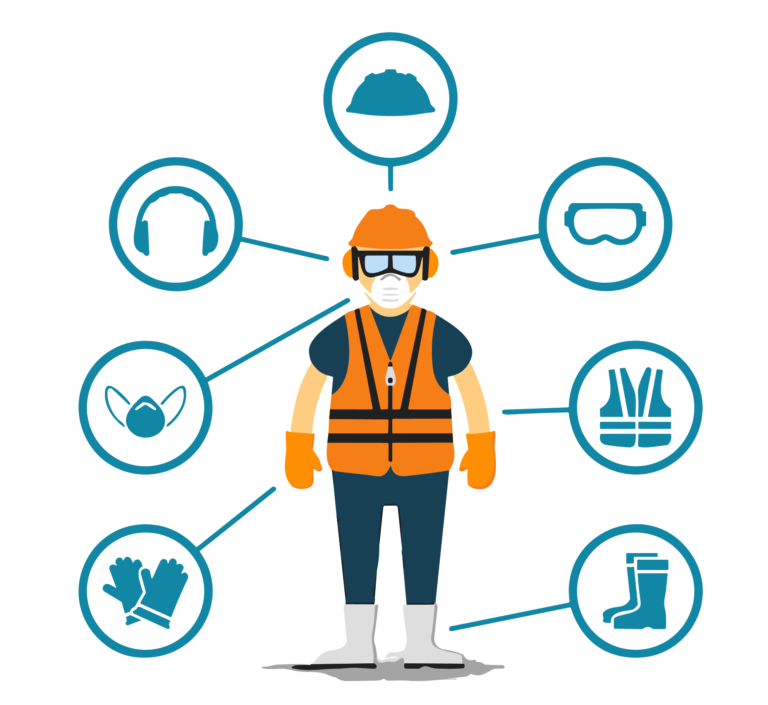
Importance of Personal Protective Equipment:
Personal protective equipment serves as a critical line of defense against various workplace hazards. By wearing PPE, workers can reduce their exposure to potential risks, such as physical injuries, respiratory problems, eye damage, and hearing loss. PPE includes a wide range of items designed to protect specific body parts or systems, including protective footwear, noise reduction devices, safety goggles, and respiratory masks. Each type of PPE serves a specific purpose and should be selected based on the nature of the job and associated hazards.
Personal protective equipment (PPE) plays a pivotal role in ensuring the safety and well-being of workers across various industries. The importance of PPE cannot be overstated, as it acts as a crucial barrier between workers and potential hazards present in the workplace.
One of the primary benefits of using PPE is the reduction of physical injuries. In industries where workers are exposed to hazards such as falling objects, sharp edges, or heavy machinery, protective footwear, helmets, and gloves provide vital protection. These items help prevent injuries such as fractures, lacerations, and punctures, safeguarding workers from immediate harm.
Respiratory problems are another significant concern in many work environments, particularly those involving airborne contaminants, dust, or hazardous substances. Respiratory masks and respirators are essential in safeguarding workers’ lungs and preventing long-term health issues. By filtering out harmful particles or chemicals, respiratory PPE ensures that workers breathe clean air, reducing the risk of respiratory illnesses and chronic conditions.
Eye protection is crucial in industries where workers are exposed to potential eye hazards, such as flying debris, chemicals, or intense light. Safety goggles or face shields shield the eyes from impact, splashes, or radiation, minimizing the risk of eye injuries, including corneal abrasions, chemical burns, or blindness. By wearing appropriate eye protection, workers can maintain their vision and prevent long-lasting damage.
Hearing loss is a prevalent occupational health issue, particularly in industries with high noise levels, such as construction, manufacturing, and aviation. Noise reduction devices, including earplugs and earmuffs, protect workers’ hearing by reducing the intensity of noise exposure. By minimizing the risk of noise-induced hearing loss, PPE for hearing protection safeguards workers’ auditory health and contributes to their overall well-being.
It is crucial to note that PPE should be selected based on the specific hazards present in the workplace. Different job roles and industries require different types of PPE to address their unique risks effectively. Employers have a responsibility to assess workplace hazards, provide appropriate PPE, and ensure that workers are trained on its correct usage. This includes educating workers on how to properly wear, adjust, and maintain their PPE to maximize its effectiveness.
In conclusion, personal protective equipment is a vital component of workplace safety. It acts as a crucial line of defense against various hazards, including physical injuries, respiratory problems, eye damage, and hearing loss. By providing and using the appropriate PPE, employers can significantly reduce the risk of workplace accidents, injuries, and long-term health issues. PPE not only protects workers but also contributes to a culture of safety, fostering a secure and healthy work environment for everyone involved.
Effective Use of Protective Equipment:
In addition to personal protective equipment, the utilization of protective gear further enhances workplace safety. Items such as gloves, helmets, caps, and covers serve as a barrier between workers and potential hazards. Gloves protect against chemical exposure, cuts, and abrasions, while helmets provide head protection against falling objects and impacts. Caps and covers shield workers from potential entanglements, entrapments, or contact with moving parts of machinery. These protective equipment items should be properly selected, fitted, and regularly inspected to ensure their optimal performance.
In addition to personal protective equipment (PPE), the effective use of protective gear plays a crucial role in enhancing workplace safety. Protective gear serves as an additional layer of defense, providing workers with specific protection against various hazards they may encounter on the job.
Gloves are an essential type of protective gear that offers protection against chemical exposure, cuts, and abrasions. Depending on the nature of the work, different types of gloves, such as chemical-resistant gloves, cut-resistant gloves, or heat-resistant gloves, should be selected to match the specific hazards present. Properly fitted gloves not only minimize the risk of direct contact with harmful substances or sharp objects but also provide dexterity and grip necessary for performing tasks effectively.
Helmets are another critical piece of protective gear that safeguards workers from head injuries. They are designed to protect against falling objects, impacts, and potential head trauma. Industries such as construction, manufacturing, and mining often require the use of helmets to mitigate the risk of severe head injuries. Helmets should be worn consistently and securely fastened to provide optimal protection. Regular inspection of helmets is necessary to ensure that they are free from cracks, deformations, or other signs of damage that may compromise their effectiveness.
Caps and covers are protective gear items that serve specific purposes in various work environments. They act as safeguards against entanglements, entrapments, or contact with moving parts of machinery. Workers in industries such as manufacturing, agriculture, or construction may use caps with chin straps to protect against hair entanglement in machinery. Covers, such as machine guards or equipment enclosures, provide a physical barrier to prevent accidental contact with hazardous areas. Regular inspection and maintenance of caps and covers are essential to ensure their integrity and functionality.
Proper selection, fitting, and regular inspection of protective gear are crucial for their optimal performance. Employers should assess the specific hazards present in the workplace and provide appropriate protective gear accordingly. It is essential to consider factors such as material quality, ergonomics, and compatibility with other PPE when selecting gear. Proper fitting ensures that the gear provides adequate coverage and protection without hindering the worker’s mobility or compromising their safety. Regular inspections and maintenance routines should be established to identify any signs of wear, damage, or degradation, and defective gear should be promptly replaced to maintain its effectiveness.
In conclusion, the effective use of protective gear, in addition to personal protective equipment, enhances workplace safety by providing an additional layer of protection against specific hazards. Gloves, helmets, caps, and covers act as barriers, shielding workers from chemical exposure, cuts, abrasions, head injuries, entanglements, and contact with moving machinery parts. Ensuring the proper selection, fitting, and regular inspection of protective gear is essential to maximize its performance and maintain a safe work environment. By prioritizing the use of protective gear, employers can significantly reduce the risk of workplace accidents and injuries, protecting the well-being of their workers.
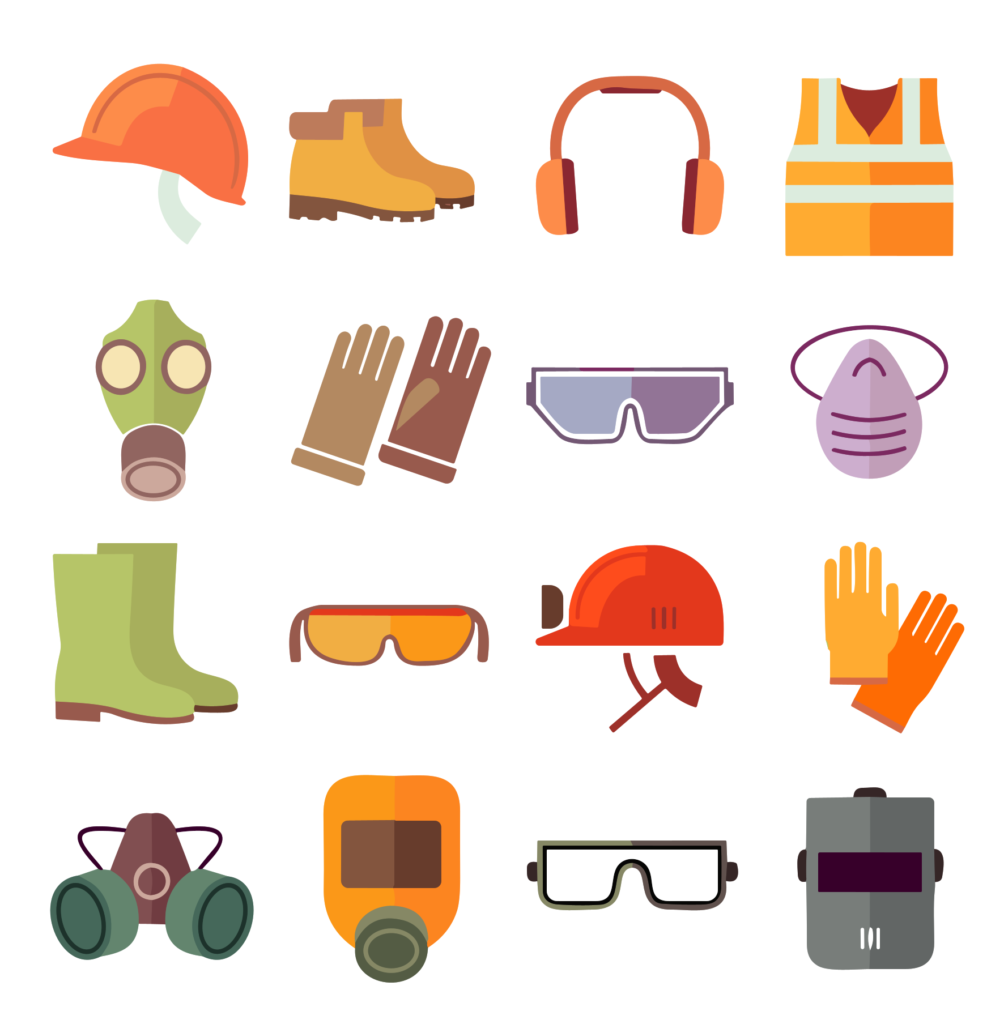
Maintenance and Regular Inspection:
To ensure the continued effectiveness of PPE and protective gear, regular maintenance and inspections are vital. Employers should establish protocols for the routine inspection, cleaning, and maintenance of safety equipment. This includes checking for any signs of wear and tear, damage, or degradation that may compromise the equipment’s functionality. Regular training should be provided to workers on how to properly use, store, and maintain their personal protective equipment. Any defective or damaged equipment should be immediately replaced to prevent potential risks and maintain a safe working environment.
Maintenance and regular inspection are essential aspects of ensuring the ongoing effectiveness of personal protective equipment (PPE) and protective gear. Employers have a responsibility to establish protocols and procedures for the routine maintenance and inspection of safety equipment, promoting a safe working environment for their employees.
Regular inspections should be conducted to identify any signs of wear and tear, damage, or degradation that may compromise the functionality of the PPE and protective gear. This includes checking for cracks, tears, broken components, or any other visible defects. Inspections should cover all aspects of the equipment, such as straps, fasteners, lenses, or other critical parts.
In addition to visual inspections, functional tests may be necessary for certain types of PPE. For example, testing the effectiveness of respirators or checking the integrity of gloves for chemical resistance may require specialized procedures. Manufacturers’ guidelines and industry standards should be followed to ensure accurate and reliable testing methods.
Regular cleaning of PPE is an important maintenance practice. Depending on the type of equipment, cleaning procedures may involve using mild detergents, disinfectants, or specialized cleaning solutions. Proper cleaning removes contaminants, dirt, or substances that may compromise the performance or hygiene of the equipment. Workers should be trained on the appropriate cleaning methods to ensure effective decontamination and maintenance.
Training plays a vital role in educating workers on the proper use, storage, and maintenance of their personal protective equipment. Clear instructions should be provided on how to inspect PPE, including what to look for and when to replace or repair damaged equipment. Workers should also be trained on how to properly store their PPE to prevent damage or contamination when not in use. Regular refresher training sessions should be conducted to reinforce these practices and address any updates or changes in equipment or procedures.
Any defective or damaged PPE should be promptly replaced to eliminate potential risks. Workers should be encouraged to report any issues with their equipment, and a system should be in place for replacing or repairing damaged items efficiently. Timely replacement or repair ensures that workers are always equipped with functional and reliable PPE, minimizing the chances of accidents or injuries.
By establishing protocols for maintenance and regular inspections, providing proper training to workers, and promptly addressing any equipment issues, employers can maintain the effectiveness of PPE and protective gear. This proactive approach ensures that workers are adequately protected and creates a culture of safety within the workplace.
Training and Education:
Equally important as the provision of PPE and protective gear is the training and education of workers on their proper usage. Employees should receive comprehensive training on the selection, fitting, and correct usage of PPE. They should be educated about the potential hazards in their work environment and the corresponding protective measures. Furthermore, workers should be informed about the importance of regular inspection, maintenance, and replacement of safety equipment.
Training and education are crucial components of ensuring the effective use of personal protective equipment (PPE) and protective gear in the workplace. It is essential for employers to provide comprehensive training to workers on various aspects of PPE to promote a safe and healthy work environment.
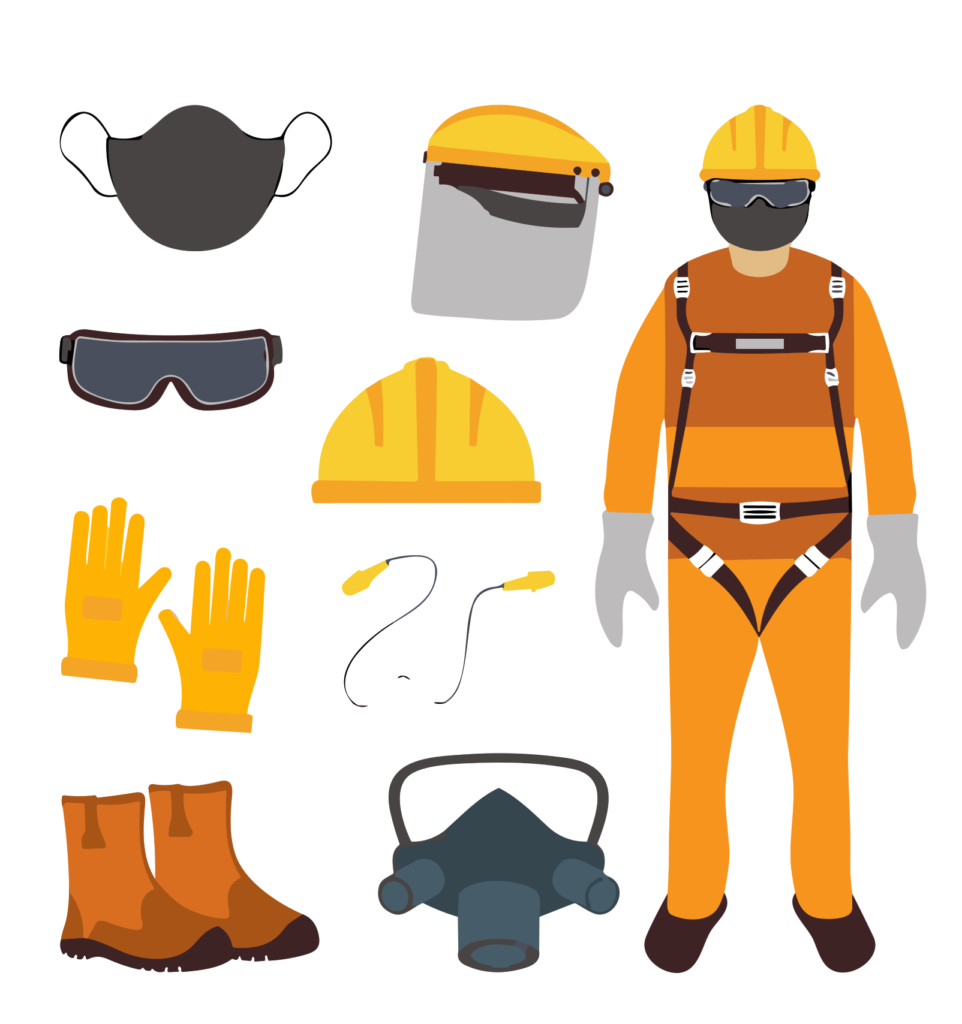
Employees should receive thorough training on the selection of appropriate PPE for their specific job tasks and potential hazards they may encounter. This includes understanding the different types of PPE available and their intended use. Workers should be educated about the specific hazards in their work environment and the corresponding protective measures required to mitigate those risks effectively.
Proper fitting of PPE is another critical aspect that should be emphasized during training. Workers need to understand how to correctly wear and adjust their protective equipment to ensure optimal protection. This includes instructions on adjusting straps, fasteners, or other components to ensure a secure and comfortable fit. Ill-fitting PPE may not provide adequate protection and can hinder the worker’s ability to perform their tasks safely and efficiently.
Training sessions should also cover the proper usage of PPE. Workers need to be educated on how to use their protective equipment correctly in various situations. This involves demonstrating the proper techniques for donning and doffing PPE, as well as any specific usage instructions for different types of equipment. Workers should understand the limitations of their PPE and be aware of when additional precautions may be necessary.
Regular inspection, maintenance, and replacement of safety equipment should also be emphasized in training programs. Workers should be informed about the importance of regularly inspecting their PPE for signs of wear, damage, or degradation. They should be trained on how to conduct visual inspections and functional tests, as well as how to properly clean and store their equipment. Additionally, workers should understand the significance of promptly reporting any issues with their PPE to their supervisors or the designated personnel.
Training and education should be ongoing processes, and regular refresher sessions should be conducted to reinforce knowledge and address any updates or changes in equipment or procedures. Employers should provide clear and accessible resources, such as written materials, visual aids, or online platforms, to support the training efforts and serve as a reference for workers.
By investing in comprehensive training and education, employers can empower their workers with the knowledge and skills necessary to effectively use PPE and protective gear. This not only enhances workplace safety but also fosters a culture of responsibility and awareness regarding personal protection.
Conclusion:
The utilization of personal protective equipment and safety gear is crucial in mitigating workplace hazards and ensuring the well-being of workers. By employing appropriate PPE, such as footwear, hearing protection, goggles, and masks, and utilizing protective gear like gloves, helmets, and covers, employers can significantly reduce the risk of accidents, injuries, and long-term health issues. Regular maintenance, inspection, and replacement of safety equipment are essential to maintain their effectiveness. With proper training and education, workers can understand the importance of using and maintaining personal protective equipment, fostering a culture of safety and creating a secure work environment for all.
