Safety Performance Monitoring and Evaluation: A Key Component of Effective Safety Management
Safety performance monitoring and evaluation are critical aspects of ensuring a safe working environment. This article explores the importance of reporting and investigating incidents and accidents, conducting safety assessments to identify weaknesses, and implementing improvements based on evaluation results. It highlights the significance of a proactive approach to safety management, emphasizing continuous improvement and the implementation of preventive measures. The article concludes by emphasizing the role of safety performance monitoring and evaluation in fostering a culture of safety within organizations.
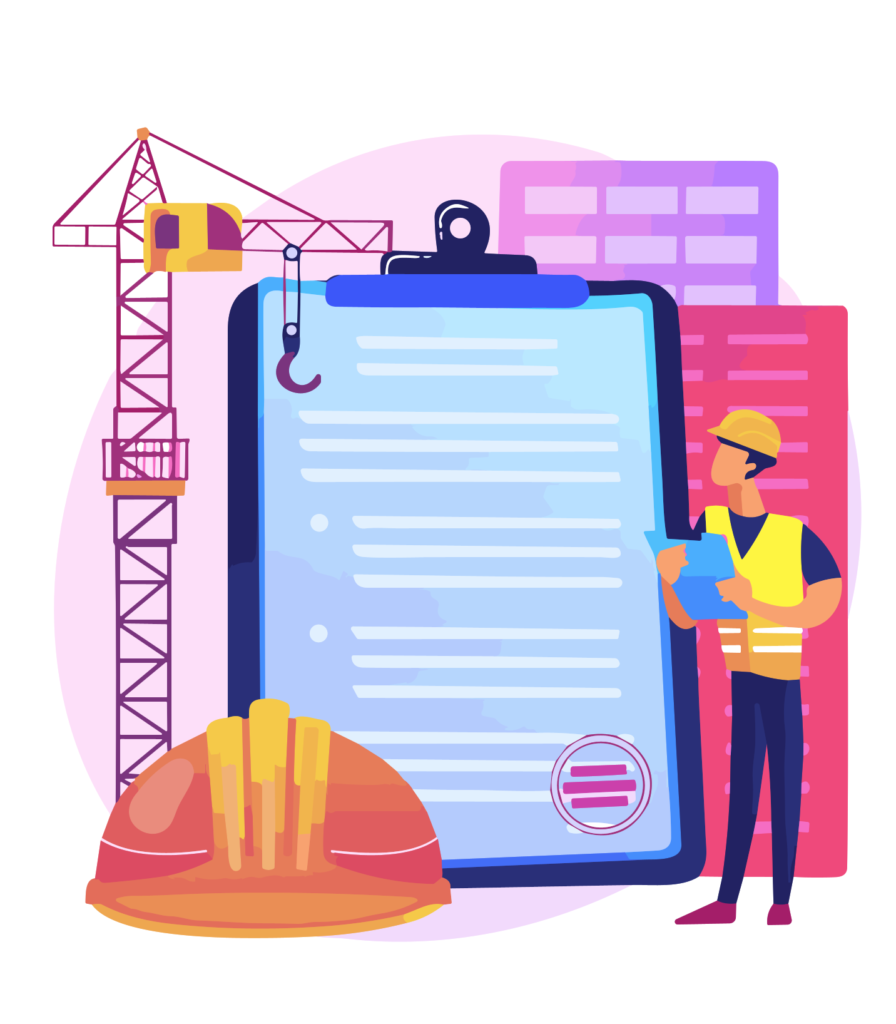
Introduction:
Maintaining a safe working environment is a top priority for organizations across various industries. To achieve this, it is crucial to establish robust safety performance monitoring and evaluation systems. This article discusses the key elements involved in this process, including incident reporting, investigation, safety assessments, and the subsequent implementation of improvements.
Incident Reporting and Investigation:
Prompt and accurate reporting of incidents and accidents is essential for understanding their underlying causes and identifying potential hazards. Organizations should establish a clear reporting mechanism that encourages employees to report incidents without fear of reprisal. A thorough investigation should follow each incident, aiming to identify root causes and contributing factors. The findings from these investigations serve as valuable input for safety improvement measures.
Prompt and accurate incident reporting and thorough investigation are crucial components of effective safety management within organizations. Establishing a clear and accessible reporting mechanism is essential to encourage employees to report incidents and accidents without fear of retaliation. It is important to create an environment where individuals feel comfortable coming forward to share their experiences and observations.
When an incident occurs, it is essential to conduct a comprehensive investigation to understand the underlying causes and contributing factors. This involves gathering evidence, interviewing witnesses, and examining relevant documents or equipment. The investigation aims to uncover root causes, which are the fundamental factors that led to the incident, as well as contributing factors, which are the conditions or actions that played a role in the event.
By analyzing the findings of incident investigations, organizations can gain valuable insights into their safety performance and identify potential hazards or weaknesses in their systems or processes. These insights serve as a basis for implementing safety improvement measures and preventive actions. It is important to note that the focus should not only be on assigning blame but also on identifying systemic issues and implementing corrective measures.
During the investigation process, it is crucial to maintain confidentiality and protect the privacy of individuals involved. This helps create a safe reporting environment and encourages open and honest communication. Additionally, organizations should establish protocols for reporting incidents to relevant regulatory bodies or authorities when required by law.
Regular monitoring and analysis of incident data can provide organizations with a broader perspective on trends and patterns. This data-driven approach enables the identification of recurring issues and areas for improvement. It also helps in setting priorities for safety initiatives and allocating resources effectively.
Furthermore, organizations should provide appropriate training and resources to employees involved in incident reporting and investigation. Training should cover incident reporting procedures, evidence collection techniques, and effective interviewing skills. This ensures that individuals responsible for conducting investigations have the necessary knowledge and skills to carry out their roles effectively.
In summary, incident reporting and investigation are essential to understand the causes of incidents, identify potential hazards, and implement safety improvement measures. By establishing a culture of open reporting, conducting thorough investigations, and using the findings to drive continuous improvement, organizations can enhance their safety performance and create a safer working environment for all stakeholders.
Safety Assessments and Weakness Identification:
Regular safety assessments are vital for evaluating the overall safety performance of an organization. These assessments involve identifying potential hazards, evaluating existing control measures, and assessing compliance with safety regulations and standards. By conducting these assessments, organizations can proactively identify weaknesses, prioritize areas for improvement, and allocate resources effectively.
Regular safety assessments are critical for organizations to evaluate their overall safety performance and ensure a safe working environment. These assessments involve a systematic and comprehensive evaluation of various aspects of safety within the organization. Here is a more expanded version of the paragraph:
Safety assessments play a vital role in identifying potential hazards, evaluating existing control measures, and assessing compliance with safety regulations and standards. These assessments should be conducted regularly and encompass all areas and processes within the organization.
- Hazard Identification:
Safety assessments involve a thorough examination of the workplace to identify potential hazards that could pose risks to employees, visitors, or the surrounding environment. This includes assessing physical hazards (such as unsafe equipment or infrastructure), chemical hazards (such as hazardous substances), biological hazards (such as pathogens), and ergonomic or psychosocial hazards (such as poor workstation design or excessive workload).
- Evaluation of Control Measures:
Once hazards are identified, safety assessments involve evaluating the effectiveness of existing control measures in place to mitigate those hazards. This includes examining engineering controls (such as safety barriers or ventilation systems), administrative controls (such as standard operating procedures or training programs), and personal protective equipment (PPE) requirements. The assessment aims to determine whether these controls are adequate, properly implemented, and consistently followed.
- Compliance with Regulations and Standards:
Safety assessments also involve evaluating the organization’s compliance with relevant safety regulations, industry standards, and best practices. This includes reviewing legal requirements, local regulations, and industry-specific guidelines. Assessments help ensure that the organization is meeting its legal obligations and following recognized standards to maintain a safe working environment.
- Weakness Identification and Prioritization:
One of the primary objectives of safety assessments is to identify weaknesses or areas for improvement within the organization’s safety management system. This may include deficiencies in control measures, non-compliance with regulations, or gaps in safety procedures. By identifying these weaknesses, organizations can prioritize areas for improvement and allocate resources effectively to address the most critical risks.
- Resource Allocation and Action Planning:
Based on the findings of the safety assessments, organizations can allocate resources, such as budget and personnel, to implement necessary improvements. Action plans should be developed to address identified weaknesses, including specific tasks, responsible parties, timelines, and performance indicators. These action plans should be regularly reviewed and updated to ensure progress is being made.
- Continuous Monitoring and Review:
Safety assessments should be an ongoing process, with regular monitoring and review. This allows organizations to track the effectiveness of implemented improvements, identify emerging risks, and adapt their safety management strategies accordingly. Continuous monitoring and review help create a culture of continuous improvement and ensure that safety remains a priority within the organization.
In conclusion, safety assessments are essential for organizations to evaluate their safety performance, identify hazards, evaluate control measures, ensure compliance, and prioritize areas for improvement. By conducting these assessments regularly and allocating resources effectively, organizations can proactively manage risks, maintain a safe working environment, and protect the well-being of their employees and stakeholders.
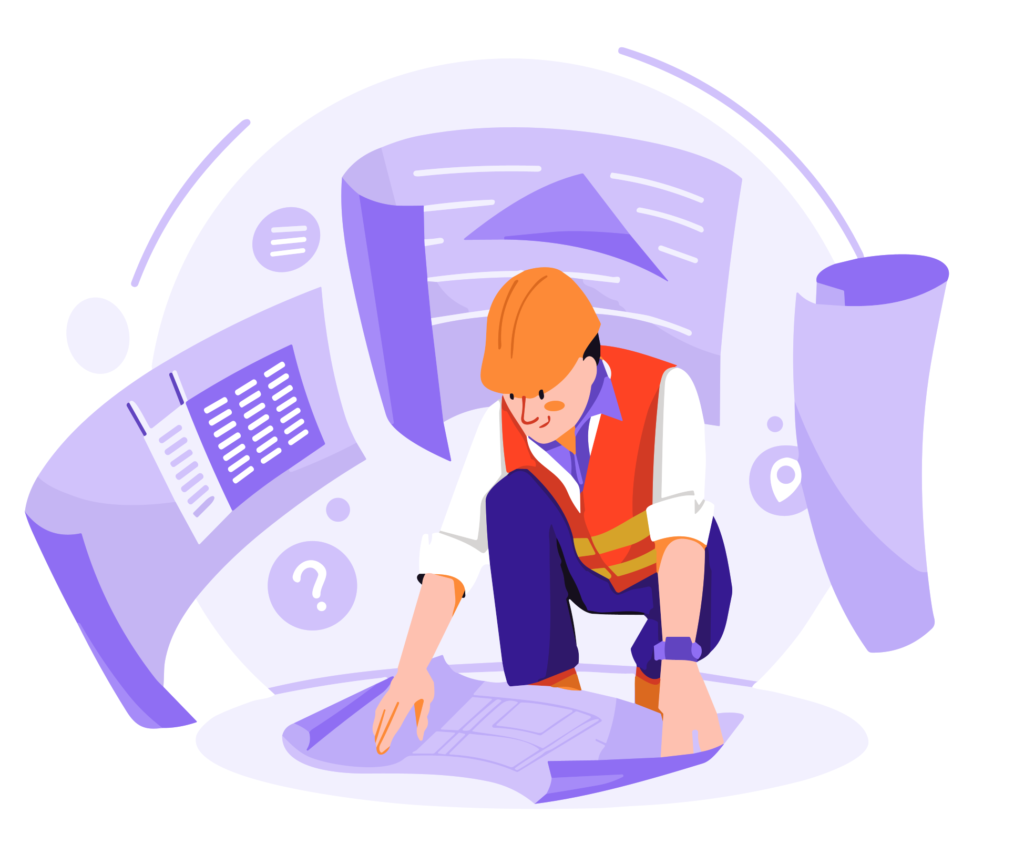
Implementing Improvements Based on Evaluation Results:
The evaluation results from incident investigations and safety assessments provide valuable insights for implementing improvements. These improvements may include revising safety procedures, providing additional training to employees, upgrading safety equipment, or implementing engineering controls. It is crucial to establish a systematic approach to prioritize and implement these improvements, ensuring that they are effectively communicated and integrated into the organization’s safety management system.
Implementing improvements based on the results of incident investigations and safety assessments is a critical step in enhancing safety within an organization. These improvements can range from revising safety procedures and protocols to providing additional training, upgrading safety equipment, or implementing engineering controls. Here is a more expanded version of the paragraph:
- Reviewing Evaluation Results:
After completing incident investigations and safety assessments, it is essential to thoroughly analyze the evaluation results. This involves reviewing the findings, identifying common trends or patterns, and understanding the underlying causes of incidents or safety weaknesses. By gaining a comprehensive understanding of the evaluation results, organizations can develop targeted improvement strategies.
- Prioritizing Improvement Measures:
Once the evaluation results have been reviewed, it is necessary to prioritize improvement measures based on the severity and potential impact of identified issues. This involves assessing the level of risk associated with each weakness and determining the resources required for implementation. Prioritization ensures that the most critical areas are addressed first, maximizing the effectiveness of improvement efforts.
- Developing Action Plans:
To implement improvements effectively, organizations should develop action plans that outline specific steps, responsibilities, timelines, and performance indicators. Action plans should be clear, measurable, and aligned with the organization’s safety goals and objectives. Involving relevant stakeholders, such as safety committees or employee representatives, can enhance the effectiveness and acceptance of the action plans.
- Revising Safety Procedures and Protocols:
One common improvement measure is revising safety procedures and protocols based on the evaluation results. This may involve updating standard operating procedures, implementing additional safety checks, or enhancing emergency response protocols. Clear and concise documentation of revised procedures is crucial to ensure that employees understand and follow the updated safety guidelines.
- Providing Additional Training and Education:
Evaluation results may indicate a need for additional training and education to address knowledge gaps or enhance safety awareness among employees. Training programs can cover a wide range of topics, such as hazard identification, safe work practices, proper use of personal protective equipment, or emergency response procedures. Training sessions should be engaging, interactive, and tailored to the specific needs of different employee groups.
- Upgrading Safety Equipment and Tools:
Evaluation results may also highlight the need for upgrading or replacing safety equipment and tools. This could involve investing in advanced technologies, improving safety features, or ensuring that equipment is properly maintained and inspected. Upgrading safety equipment not only enhances worker protection but also demonstrates the organization’s commitment to safety.
- Implementing Engineering Controls:
In some cases, evaluation results may indicate the need for engineering controls to eliminate or minimize hazards. This could involve redesigning workspaces, installing safety barriers or guards, or automating processes to reduce human exposure to risks. Engineering controls aim to create a safer work environment by eliminating or reducing hazards at the source.
- Communication and Integration:
To ensure the successful implementation of improvements, effective communication and integration into the organization’s safety management system are crucial. This involves clearly communicating the rationale behind the improvements, providing training and guidance on their implementation, and fostering a culture of safety throughout the organization. Regular communication channels, such as safety meetings, newsletters, or intranet platforms, can facilitate the dissemination of information.
- Monitoring and Evaluation:
Once improvements are implemented, it is essential to monitor their effectiveness and evaluate their impact on safety performance. This can be done through ongoing data collection, incident tracking, and periodic safety audits. Regular evaluation allows organizations to assess the success of implemented improvements, identify any unforeseen consequences, and make necessary adjustments to further enhance safety.
In conclusion, implementing improvements based on evaluation results is a crucial step in enhancing safety within an organization. By revising safety procedures, providing additional training, upgrading equipment, and implementing engineering controls, organizations can address identified weaknesses and create a safer working environment. Effective communication, integration into the safety management system, and ongoing monitoring and evaluation are key to ensuring the successful implementation and continuous improvement of these measures.
Continuous Improvement and Preventive Measures:
Safety performance monitoring and evaluation should not be viewed as one-time activities but rather as an ongoing process of continuous improvement. By analyzing trends and patterns in incident data, organizations can identify recurring issues and develop preventive measures to address them. This proactive approach helps mitigate risks before incidents occur, further enhancing safety performance.
Continuous improvement and the implementation of preventive measures are essential for maintaining and enhancing safety performance within organizations. Rather than treating safety as a one-time activity, it should be viewed as an ongoing process. Here is a more expanded version of the paragraph:
- Safety Performance Monitoring:
To achieve continuous improvement, organizations should establish a robust safety performance monitoring system. This involves collecting and analyzing data related to incidents, near-misses, safety audits, and other relevant safety indicators. By monitoring safety performance over time, organizations can identify trends, patterns, and areas that require improvement.
- Trend Analysis and Identification of Recurring Issues:
Through careful analysis of safety data, organizations can identify recurring issues or patterns that contribute to incidents or near-misses. This includes examining the root causes, common contributing factors, and systemic weaknesses that lead to these incidents. By understanding these recurring issues, organizations can develop targeted strategies to address them effectively.
- Implementing Preventive Measures:
Once recurring issues are identified, organizations can implement preventive measures to mitigate risks and prevent future incidents. This proactive approach focuses on eliminating or minimizing hazards before they result in accidents or injuries. Preventive measures may include revising procedures, providing additional training, enhancing equipment or facility design, or implementing safety controls to address identified weaknesses.
- Risk Assessment and Hazard Identification:
Continuous improvement also involves conducting regular risk assessments and hazard identification processes. This helps organizations proactively identify potential hazards, evaluate associated risks, and implement appropriate control measures. By addressing hazards before incidents occur, organizations can reduce the likelihood of accidents and create a safer working environment.
- Employee Engagement and Feedback:
Engaging employees in the continuous improvement process is crucial. Employees are often the ones who are directly involved in day-to-day operations and can provide valuable insights into safety issues and potential improvements. Creating channels for employees to provide feedback, suggestions, and report near-misses encourages a culture of safety and fosters a sense of ownership and responsibility among all members of the organization.
- Learning from Best Practices and Industry Standards:
Organizations can also learn from best practices and industry standards to drive continuous improvement. Benchmarking against other organizations within the same industry or seeking guidance from professional associations can provide valuable insights into effective safety management strategies. By adopting proven practices and implementing industry standards, organizations can enhance their safety performance.
- Training and Development:
Continuous improvement requires investing in the training and development of employees. Providing ongoing safety training helps employees stay up to date with the latest best practices, regulations, and procedures. Regular training sessions, refresher courses, and toolbox talks can reinforce safety awareness, promote a safety-conscious culture, and equip employees with the knowledge and skills necessary to identify and address safety issues.
- Regular Review and Evaluation:
To ensure the effectiveness of continuous improvement efforts, organizations should regularly review and evaluate their safety management system. This includes periodically assessing the implemented preventive measures, analyzing the impact of improvements, and identifying areas that require further attention. Regular review and evaluation provide opportunities to adjust strategies, address emerging risks, and continuously enhance safety performance.
- Management Commitment and Support:
Continuous improvement in safety requires strong management commitment and support. Leaders must prioritize safety as a core value and actively promote a culture of continuous improvement. By providing the necessary resources, setting clear expectations, and actively participating in safety initiatives, management plays a critical role in driving continuous improvement efforts.
In conclusion, continuous improvement and the implementation of preventive measures are essential for maintaining and enhancing safety performance within organizations. By monitoring safety performance, analyzing trends, implementing preventive measures, and engaging employees in the process, organizations can proactively mitigate risks and create a safer working environment. Continuous improvement requires ongoing commitment, regular evaluation, and a culture that values safety at all levels of the organization.
Fostering a Culture of Safety:
Safety performance monitoring and evaluation play a significant role in fostering a culture of safety within an organization. When employees see that incidents are thoroughly investigated, improvements are implemented, and their input is valued, they are more likely to actively engage in safety practices and contribute to a safer work environment. Organizations should encourage open communication, provide safety training and education, and recognize and reward proactive safety behaviors.
Fostering a culture of safety is crucial for creating a work environment where safety is a core value and all employees actively participate in maintaining a safe workplace. Safety performance monitoring and evaluation play a significant role in this process. Here is a more expanded version of the paragraph:
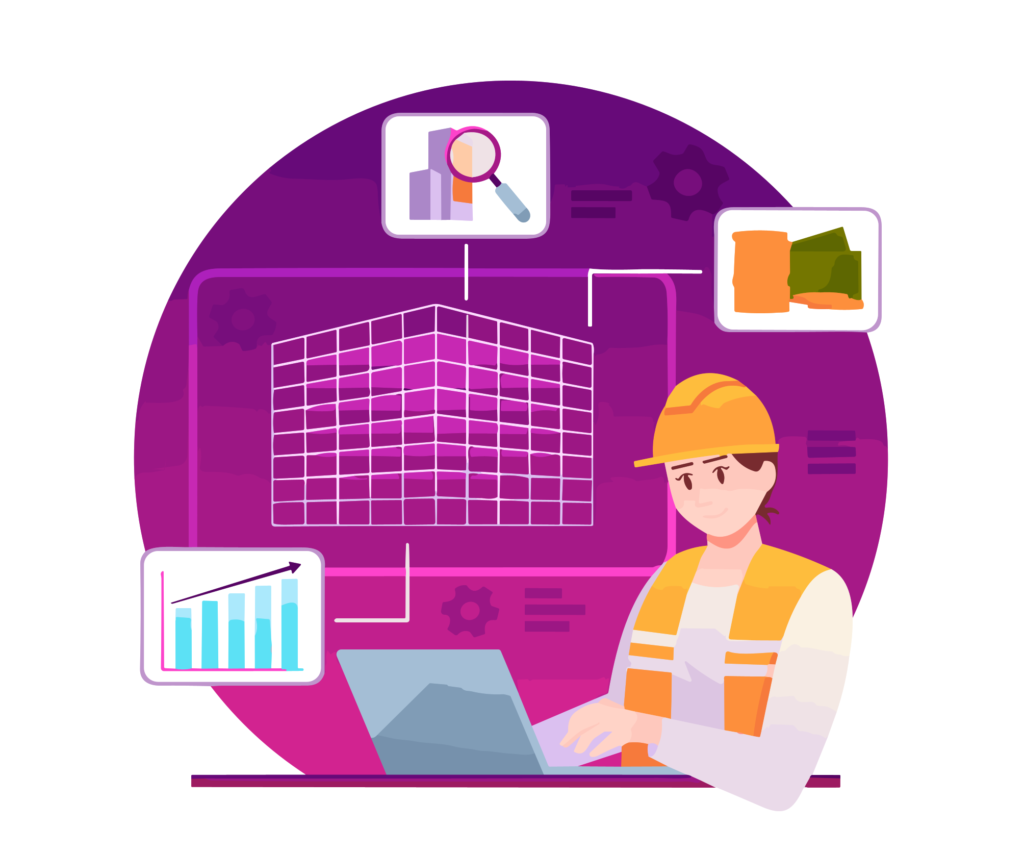
- Leadership Commitment:
Fostering a culture of safety starts with strong leadership commitment. Leaders should prioritize safety as a fundamental value and demonstrate their commitment through their actions. This includes allocating resources for safety initiatives, actively participating in safety programs, and promoting a positive safety culture throughout the organization.
- Open Communication:
Open and effective communication is key to fostering a culture of safety. Organizations should encourage employees to report safety concerns, near-misses, and potential hazards without fear of reprisal. Establishing confidential reporting mechanisms and ensuring that reported issues are addressed promptly and transparently builds trust and encourages employees to actively engage in safety practices.
- Employee Involvement and Empowerment:
Employees play a vital role in creating a safe work environment. Organizations should actively involve employees in safety programs, committees, and decision-making processes. By seeking their input, considering their perspectives, and involving them in the development of safety policies and procedures, employees feel empowered and take ownership of safety initiatives.
- Safety Training and Education:
Providing comprehensive safety training and education is essential for fostering a culture of safety. Organizations should ensure that employees receive regular training on safety protocols, hazard recognition, emergency response procedures, and the proper use of personal protective equipment. Ongoing education helps employees stay informed about evolving safety practices and reinforces the importance of safety in their daily work.
- Recognition and Rewards:
Recognizing and rewarding proactive safety behaviors encourages employees to actively engage in safety practices. Organizations should establish recognition programs that acknowledge individuals or teams for their contributions to safety, such as reporting near-misses, suggesting improvements, or demonstrating exemplary safety practices. Celebrating these achievements reinforces the culture of safety and motivates others to follow suit.
- Continuous Improvement:
Fostering a culture of safety requires a commitment to continuous improvement. Organizations should encourage employees to provide feedback, suggestions, and ideas for enhancing safety. Regularly reviewing and evaluating safety practices, implementing improvements based on employee input, and communicating the outcomes of safety performance monitoring and evaluation processes demonstrate a commitment to continuous learning and improvement.
- Leading by Example:
Leaders and supervisors should lead by example when it comes to safety. By consistently following safety procedures, using personal protective equipment, and actively participating in safety programs, they set a positive example for employees. When employees see their leaders prioritizing safety, they are more likely to emulate those behaviors and make safety a personal and collective responsibility.
- Safety Integration:
Integrating safety into all aspects of the organization’s operations is crucial for fostering a culture of safety. Safety considerations should be incorporated into planning, design, procurement, and decision-making processes. By making safety an integral part of every task and project, organizations demonstrate a commitment to the well-being of their employees and create a work environment where safety is at the forefront.
- Continuous Learning and Awareness:
Promoting continuous learning and awareness about safety is essential. Organizations should regularly share safety-related information, such as incident investigation findings, lessons learned, and best practices. Conducting safety drills, toolbox talks, and safety campaigns helps reinforce safety knowledge, raise awareness, and ensure that safety remains a top priority for all employees.
Fostering a culture of safety requires leadership commitment, open communication, employee involvement, comprehensive training, recognition of proactive behaviors, continuous improvement, leading by example, safety integration, and continuous learning. By embracing these elements, organizations can create a work environment where safety is valued, employees are empowered, and everyone actively contributes to a safer workplace.
Conclusion:
Safety performance monitoring and evaluation are integral components of effective safety management systems. By establishing robust incident reporting and investigation processes, conducting safety assessments, and implementing improvements based on evaluation results, organizations can continuously enhance their safety performance. This proactive approach not only minimizes risks and reduces incidents but also fosters a culture of safety, ensuring the well-being of employees and the long-term success of the organization.
